Lack of use, maintenance, leading to glitches in ‘Make in India’ ventilators
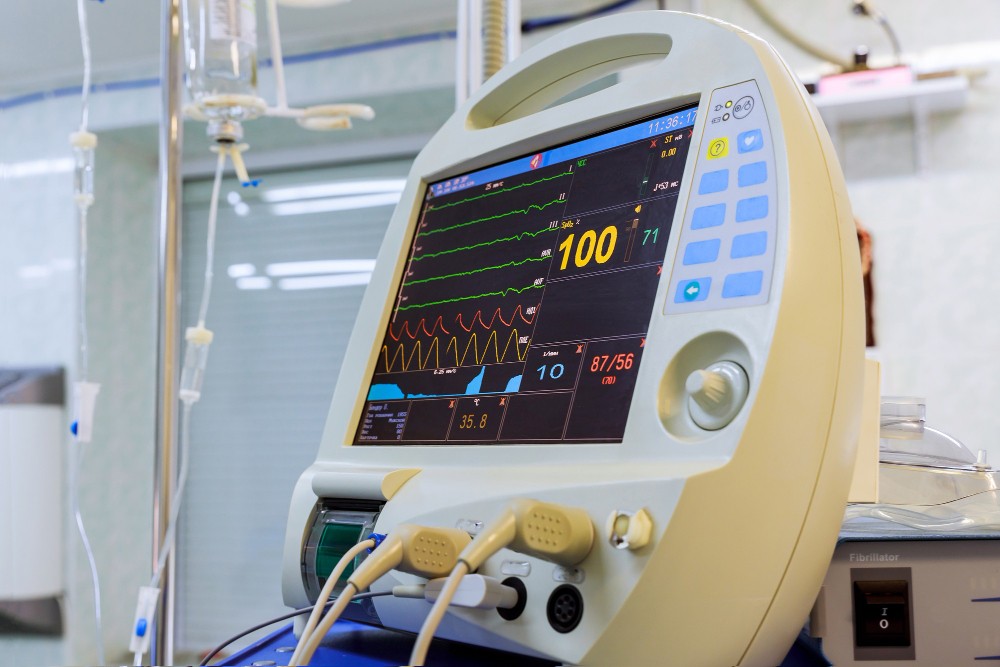
Representative Image | Freepik
Representative Image | Freepik
New Delhi | Lack of proper use and timely maintenance of ‘Make in India’ ventilators — that help you breathe or breathe for you — is resulting in glitches in the machine amid the Covid crisis, creating another challenging situation for the Centre.
Despite instructions given in the user manual, detailed guidelines issued to ventilator users regarding infrastructure requirements, proper usage and maintenance of the CV200 ventilators, “many hospitals or medical colleges are not following these”, said sources.
Flow sensors, bacteria filters and HME filters are not being changed by the hospital authorities as per the prescribed norms, or the ventilators are being used without these important consumable items.
Such lapses have caused serious concern when the Central government has been centrally procuring and providing states and Union Territories (UTs) or central hospitals or institutes with essential medical devices including ventilators since April 2020 to augment the existing hospital infrastructure.
The Union Health Ministry on Thursday posed pointed questions to a few such hospitals and medical colleges in Punjab, saying “they have been, instead, raising the issue of ventilators being non-functional without any basis”.
One such case was reported from the GGS Medical College and Hospital, Faridkot, Punjab where several ventilators were lying unused as a result of technical glitches due to lack of proper maintenance.
The hospital later raised the issue that there were technical glitches in the ‘Made in India’ ventilators due to poor service by the manufacturer after sales.
Ministry has said that a few reports were also published in media, clarifying “these reports seem to be unfounded, not having the full information on the matter”.
With reference to the recent media report regarding 71 of 80 AgVa Healthcare make ventilators being non-functional or faulty at the GGS Medical College and Hospital, the Ministry clarified 88 ventilators have been supplied by Bharat Electronics Limited (BEL) and five by AgVa.
After successful installation and commissioning, the Ministry said, these ventilators were provided with Final Acceptance Certificate by the hospital authorities.
BEL has informed that bulk of the ventilators at GGS Medical College Hospital (GGSMCH) are not faulty, the Ministry said. “Their engineers have visited the Medical College on different occasions in the past to address the complaints received and carried out minor repairs required promptly. They have even conducted repeated demonstrations of the functioning of the ventilators to the staff over there.”
It was observed that there are issues and problems with the infrastructure in GGSMCH including non-availability of required pressure in the central oxygen gas pipelines, said the Ministry.
“Further, the consumables like flow sensors, bacteria filters and HME filters are not being changed by the hospital authorities as per the prescribed norms, or the ventilators are being used without these important consumable items.
“Maintenance of correct gas pressures (difference between air pressure and oxygen pressure cannot be more than 10 PSI) and use of proper consumables are essential requirements, without which performance of CV200 ventilators is not guaranteed,” said the Ministry.
Furthermore, BEL engineers visited GGSMCH again on Wednesday and made five ventilators functional only by replacing a few consumables and demonstrated their optimum performance to the GGSMCH authorities, thereby, further making it evident that when operated properly, the ventilators will provide reliable performance.
The Central government has been supplying these ventilators supported by the PM CARES fund to hospital and medical colleges in states and UTs.
Besides, there are a few states which have received the ventilators but are yet to get these installed in their hospitals.
The Union Health Secretary has written to seven such States on April 11 and again on May 9 which still have more than 50 ventilators lying uninstalled with them for the last 4-5 months.
“They have been requested to get the installation expedited so that the ventilators can be put to optimal use.”
In addition, the Union Health Ministry had written to the states and UTs to contact ventilator manufactures on helpline numbers which are also available on the ventilators in the form of stickers.
In addition, information has again been provided of state wise Whatsapp groups created with the concerned nodal officers of the states and UTs, representatives of the user hospitals and technical teams of the manufacturers in order to address any technical issues in real time.
The Centre has also shared dedicated email IDs of the ventilator manufacturers with the states and UTs in case they get any report regarding glitches in the machine.
Ventilators were available in very limited numbers in government hospitals across the country at the beginning of the Covid pandemic last year. Moreover, very limited manufacturing of ventilators was taking place in the country and most of the suppliers abroad were not in a position to make supplies of ventilators in large quantities to India.
That is when the local manufacturers were encouraged to produce “Make in India” ventilators to address the huge projected demand of the country and orders placed on them. Many of them were first time manufacturers of the ventilators.
The ventilator models went through rigorous screening, technical demonstration and clinical validation process in the very limited time available for the same, through domain knowledge experts, and after their approval, these were put into supplies.
By IANS
The English Post is on Telegram, click to join for regular news updates